Flowrence®
Helping the leading catalyst suppliers and research institutes developing better and more efficient catalysts with the world's best high throughput technology Our technologyContact usSystems Installed
Years of Innovation
Proven Applications
Patents
Highest Data Quality
Reproducible results with accurate microfluidics distribution. Large isothermal zone with perfect catalyst-feed contacting.
Unmatched Accuracy
Proven Applications
Proven Flowrence® technology broadly used with multiple applications thanks to decades of research and development.
Safe to Operate
Inherently safe small-scale reactor technology with minimal chemicals hold up with very fast flushing times. Easy to operate <1 FTE required.
Validated by Customers
Flowrence® technology extensively used by catalyst suppliers and research institutes to accelerate their catalyst R&D.
Fast Screening
Reduced time-to-market with high throughput testing for process optimization and catalyst screening.
Lower Costs
Small Footprint
Smallest footprint in the market with low infrastructure costs. Increase the number of reactors in your lab with minimal space required.
We provide our customers the world's most high throughput technology powered by decades of research
Flowrence® Products
4 Reactors
16 Reactors
16 Reactors
Key technology features
Microfluidics distribution
Single glass chip for 16-reactors with 0.5% RSD, offers unmatched reactor-to-reactor repeatability. Easy exchange for different operating conditions.
Tiny-Pressure
Modular, compact, and easy exchange of glass-chips, with integrated pressure indicators.
Tube-in-tube reactor
Easy and quick reactor exchange system. Possibility to use quartz reactors at high pressure.
EasyLoad®
Unique and easy-to-use reactor closing system. “Ready-to-go” approach without leak testing required.
Full particles and powder loading
No dead-zones, no bed packing or distribution effects. No variability in reactor loading. Small volumes, no compromises.
FlowPro Software
Software purposely build for high throughput systems. Full integration of online and offline data.
Reactor pressure control
The most accurate and stable pressure regulator for 16-reactors, just ±0.5bar RSD.
Active liquid distribution
The most accurate liquid distribution for 16 reactors with active control. Reactor-to-reactor 0.5% RSD.

Individual temperature control
Flexibility in test design with independent Reactor Temperature Control (iRTC).
Automated liquid sampling
Programmable, fully automated liquid product sampling robot for 24/7 hands-off operation.
Proven applications with the Flowrence®
Discover how our customers are leveraging Artificial Intelligence with the Flowrence®
Argonne National Lab 16-reactors Flowrence® XR
Avantium’s 16-reactor fixed bed Flowrence® XR unit was used to study the deposition of 23 different metallic precursors for propyne dimerization to hexadienes in a high-throughput data-driven campaign. A combination of high throughput experiments with computational and machine learning approaches were imperative to finding optimized reaction conditions.
Recent case studies
Avantium’s microfluidic distribution: A Novel technology for high-throughput catalysis
How microfluidic chips enable precise and accurate control of gas and liquid flows in parallel reactors One of the challenges in high-throughput catalysis is the distribution of gas and liquid flows to multiple reactors, while ensuring uniform and stable flow rates...
High-throughput catalyst testing in our laboratories tailored for any R&D stage
In our laboratories in Amsterdam, we offer more than 800 reactors dedicated to catalyst testing. These reactors include a variety of high-throughput, multi-parallel catalyst testing platforms, in both fixed-bed and batch, ensuring high-quality, industrially scalable...
Reactor-to-reactor repeatability
An important quality criteria in parallelized reactors systems is reactor-to-reactor repeatability. A good repeatability is achieved when reactors loaded with the same catalyst system yield the same results. This means that the test results and the differences (in...
See what our customers are saying


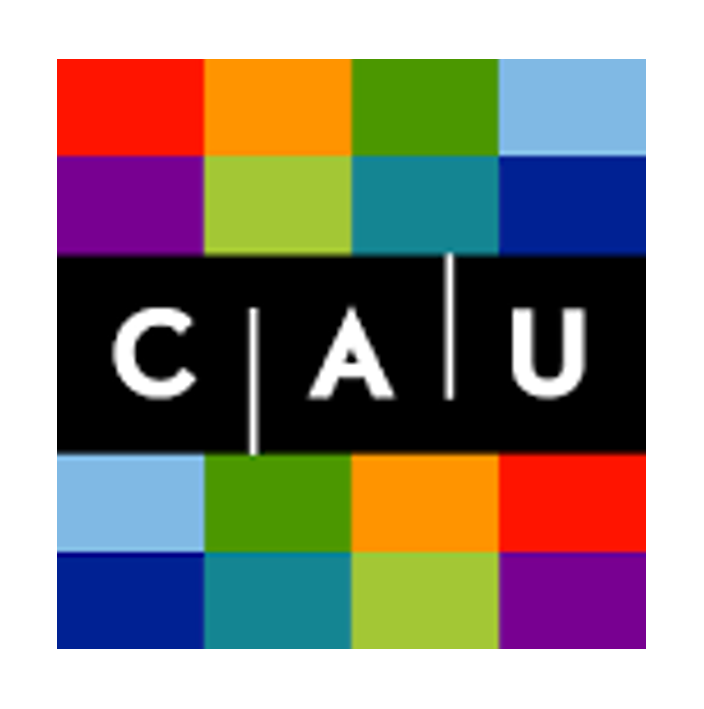
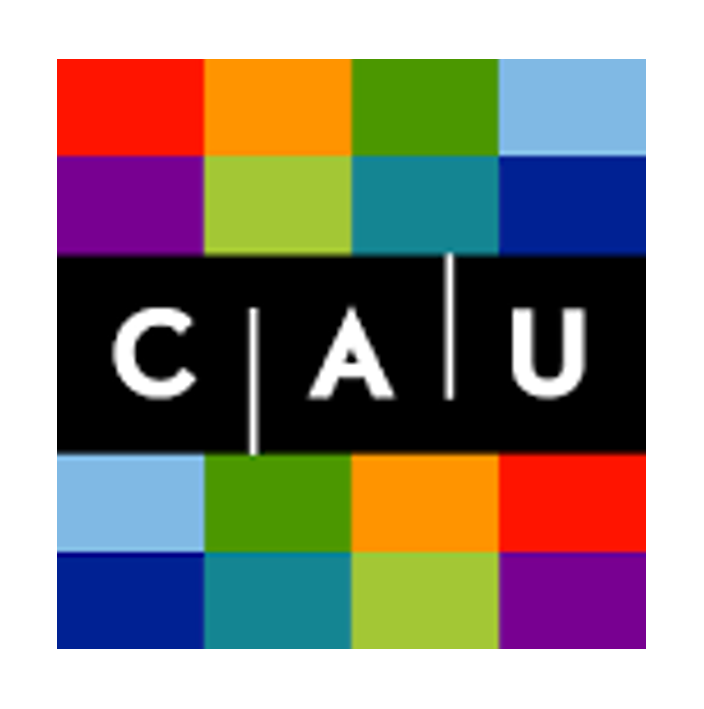
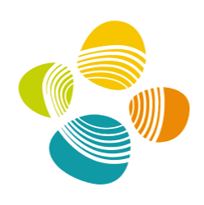
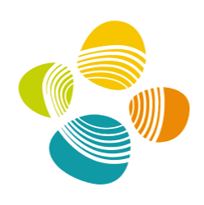
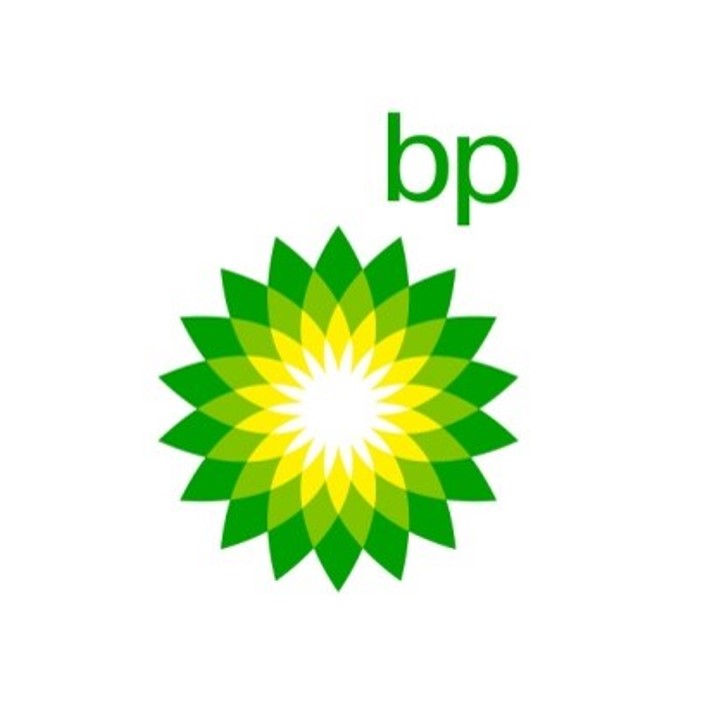
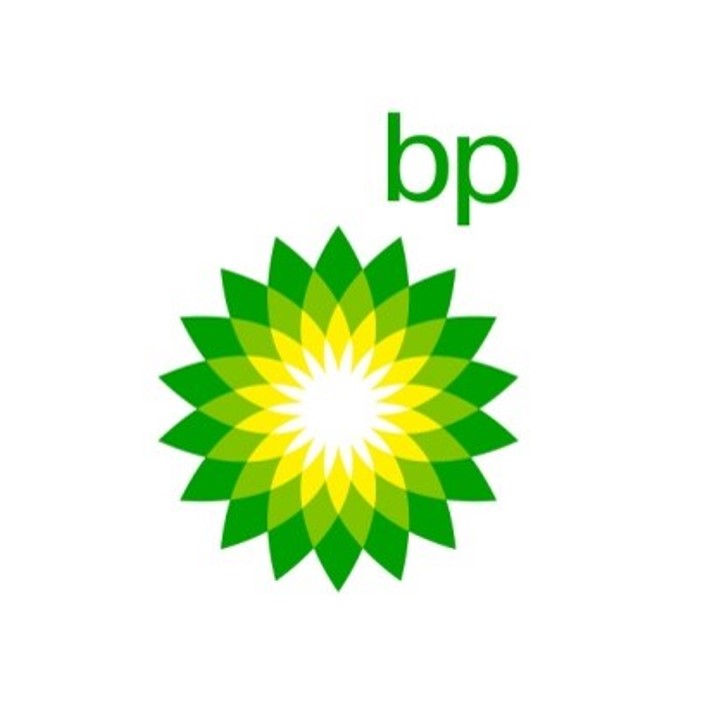
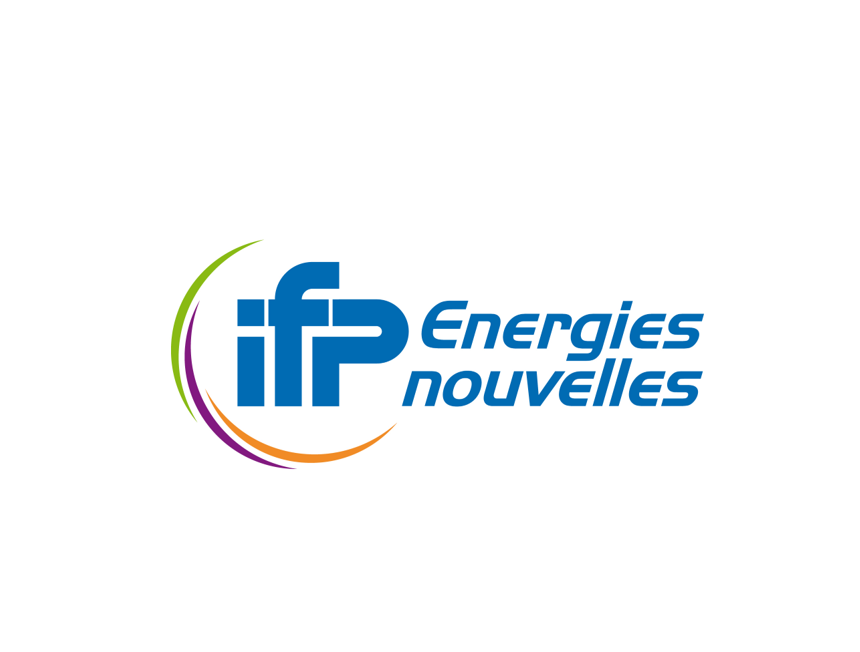
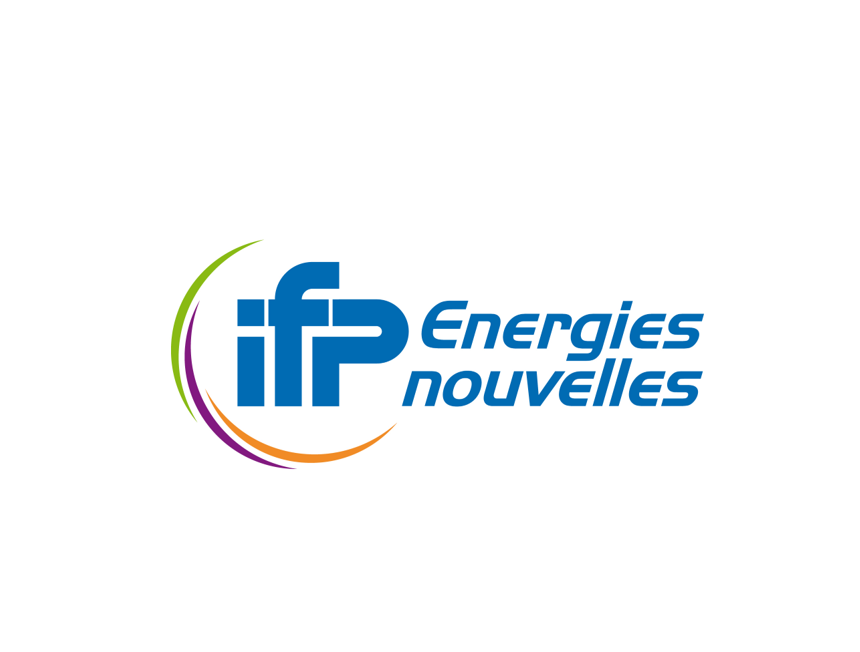
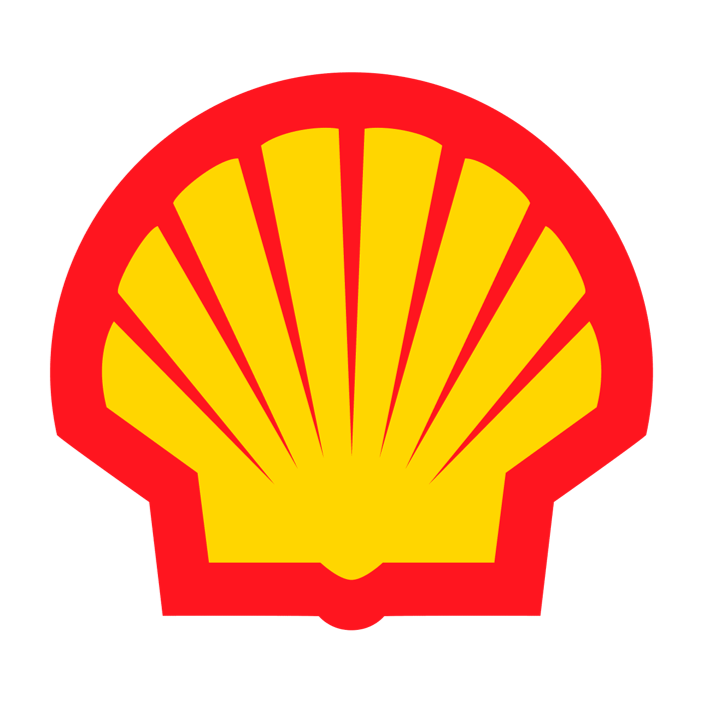
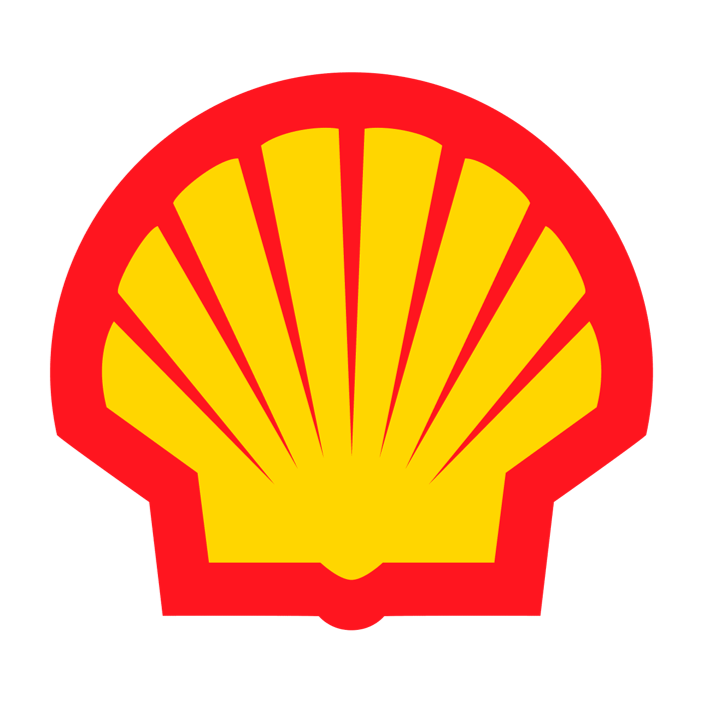